Is your Quality Team really up to the task?
by Les Sinnock, Lead Quality Lab Technician, Goodwin University
Now that we have passed through the eye of the needle and are coming out the other side of the COVID-19 pandemic, it may be time to reassess your quality team’s skill level. After all, if the measurements they make on a daily basis are inaccurate, you may be either failing parts made that should pass, or worse yet, shipping bad parts that passed inspection. Either way, you have either a high scrap rate or escapes that may cost you your company’s reputation and potentially your ability to land lucrative contracts.
How can you be sure if your team is up to the task?
One of the best tools out there is the Gauge R&R statistical tool. This tool asks two to three associates to measure one feature, three to five times, on each of 10 randomly made identical parts, using the same measurement tool (micrometer, for instance). The software, which is largely a glorified Excel spreadsheet, then uses statistical tools to evaluate whether or not your measurement system is adequate and reliable. The tool further breaks down whether the problem lies with the operator(s) or with the measurement tool. The results are both numerical and graphical. This helps to highlight if there are training issues that need to be addressed or whether the tools used for measurement aren’t up to the task (using a caliper when a micrometer should be used, etc.).
How do I get a Gauge R&R analysis?
Gauge Repeatability and Reliability analysis are available publicly through software such as Minitab or may be found on the Internet. Some training may be needed to reach an understanding of how to administer the test and how to interpret the results. Goodwin University, for example, offers training in this area and will freely give their software to companies attending the training. Should you decide to go it alone without training, you may find there is a learning curve to doing the gauge study correctly and that may have an impact on the outcome. If your results show that your measurement systems aren’t up to snuff, you then have to address the problem areas. If it’s a tooling issue, you should be able to either upgrade your tooling or switch tooling to achieve greater precision.
What if the problem is with my quality or machining associates?
Training or re-training may be the key to success here. Adding periodic refresher training can help to minimize bad habits, lost abilities, or bias. This is especially true in businesses that rely on what we call “tribal knowledge.” Tribal knowledge is simply information being passed down by other workers, whose intent is to help others out, but who often pass bad information or teach shortcuts that undermine proper usage. If you want your workers to perform tasks a certain way, it is best to have standardized methods. Reinforcing these methods through regular training sessions will improve outcomes. Even seasoned workers can benefit from this, as often little bits of information are lost over time.
So what should I do to start a training cycle?
If you have in-house trainers who have the requisite experience, have them create a training calendar that works through all of the topics needed to train-up or stay sharp. If you don’t have an in-house trainer, there are private consultants that can work with your company to provide direction, or you can reach out to an institution of higher education that specializes in continuing education for corporate clients. Goodwin University offers a wide variety of continuing education courses to companies throughout Connecticut. The courses are designed to up-skill incumbent workers. So if you are promoting within, in an effort to fill positions, or are hiring off the street, these courses will help to bring your workers’ skills to a level at which their productivity increases.
In regard to quality measurement work, in addition to the Gauge R&R training Goodwin offers targeted training in the use of quality measurement tools in a setting that includes both a lecture and the use of the tools (Metrology I). Additionally, a second course has been created with very little lecture but increased work with the measuring tools and parts and our Gauge R&R tool to understand more about each person’s measuring capability. Statistics are displayed for everyone to observe, then targeted training helps workers hone their craft through use of a hands-on clinic. Measurements are done once again to validate improvements (Metrology II Lab & Clinic).
With all this in mind, you should ask yourself: Is my quality department fully capable? Are my machining associates performing setup correctly and are they using their measurement tools correctly? If there you have any doubt, it could be costing you more in the long run.
The Goodwin University Advanced Manufacturing Worker Training programs have trained 2,300 workers at more than 65 manufacturing companies in Connecticut. More information on training offerings can be found at https://www.goodwin.edu/majors/manufacturing/worker-training
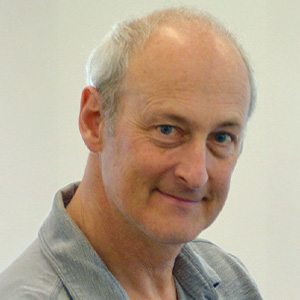
Les Sinnock is the Lead Quality Lab Technician and Continuing Education Instructor at Goodwin University’s School of Business, Technology, and Advanced Manufacturing. He is an industry veteran of 42 years and has been employed in the engineering technical trades at electronics, automation, brewing, R & D of fuel cell, and space flight technologies.
lsinnock@goodwin.edu