Are you Practicing Continuous Quality Improvement?
by Les Sinnock, Lead Quality Lab Technician, Goodwin University
One of the ways that you can enhance the profitability of your company is to add a program of Continuous Quality Improvement. This strategy is also known as “Kaizen” and is usually kicked off with a directive from upper management that filters down through supervision to the workers. Some training is often required to ensure that everyone is on board with the ideas and activities. Kaizen is an all-encompassing term that covers topics such as TPM, kanban, productivity improvement, and a suggestion system to name a few.
What is Kaizen?
Kaizen, which means “change for the better,” has helped Japanese industries to generate a process-oriented way of thinking and to develop strategies that assure continuous improvement involving people at all levels. The strategy is that not a day should go by without some kind of improvement being made somewhere in the company.
Kaizen vs. innovation
In the West, we tend to think of opportunities to improve as tasks of innovation: spend big dollars to buy a new piece of equipment that will improve production and profitability. This often interrupts production briefly to install. It is dramatic, high-cost, high-risk, and often requires technology training. Kaizen, on the other hand, is an incremental improvement process that is undramatic, low-cost, low-risk, and most often requires only human effort.
How can this work?
Using something as simple as a suggestion box, a semi-skilled worker who works at a machine following instructions may discover a more effective way of accomplishing a particular task. As workers become more proficient and gain greater skills, their ideas may increase in greater numbers and greater validity. These ideas can be reviewed, solutions tested, and, if valid, incorporated into the standard work.
Who would be involved in Kaizen?
Every worker within your shop — from management and office workers to engineers and shop workers — can be involved. Having a Kaizen champion can help to drive the effort and ensure that the improvements are being tested and implemented. Some objections may come from those who believe a procedure can’t be improved upon because “this is how we have always done it,” or that an idea is too immature to test. As it turns out, no idea is a “bad” and can ultimately lead to an even better solution.
What happens if I don’t make improvements to my processes?
Your competitors are continually implementing improvements to make their companies more efficient and profitable, so if you aren’t moving forward, you are sliding backward! Kaizen helps you to make inexpensive improvements a reality.
The Goodwin University Advanced Manufacturing Worker Training programs have trained 2,300 workers at more than 65 manufacturing companies in Connecticut. More information on training offerings can be found at https://www.goodwin.edu/majors/manufacturing/worker-training.
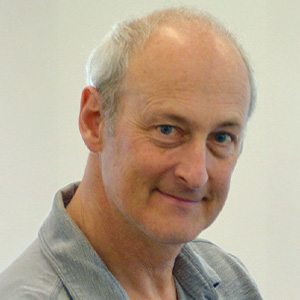
Les Sinnock is the Lead Quality Lab Technician and Continuing Education Instructor at Goodwin University’s School of Business, Technology, and Advanced Manufacturing. He is an industry veteran of 42 years and has been employed in the engineering technical trades at electronics, automation, brewing, R & D of fuel cell, and space flight technologies.
lsinnock@goodwin.edu