by Les Sinnock, Director of Advanced Manufacturing Labs, and Kyle Zachary, Assistant Professor, Continuing Education, Goodwin University
The year 2021 was eventful in Connecticut and at Goodwin University. While still a COVID-impacted time with the associated disruptions and inconveniences, it was also a year that saw a large increase in training activity from 2020. We also observed a shift in our conversations with manufacturing companies from a focus on training incumbent workers to simply getting new hires, trained or not, in the door. These cumulative trends are now guiding our training efforts going forward into 2022.
As 2021 came to a close, we compiled Continuing Ed training statistics including a year-over-year comparison of training activity. We also mapped the geographic distribution of the companies who have accessed Goodwin training. After launching the incumbent worker training options in 2016, the Continuing Ed program hit its pre-pandemic stride in 2018 (running 81 workshops with 791 attendees) and 2019 (58 workshops with 785 attendees). All indications in early 2020 were for another strong year, but the pandemic ultimately restricted training activity to 14 workshops, training 140 workers.
Though things started slowly in 2021, the second half of the year saw a significant rebound in training, and we closed out the year having run 40 workshops with 479 workers trained. In addition, 2021 saw the introduction of a new online training platform as an alternative to live in-person workshops. The online content was built from the 180 Skills training platform, with courses constructed to meet the skills gaps Connecticut manufacturers are currently facing. The pandemic also marked our first foray into delivering live workshops via Zoom. We also ran the first in an ongoing series in Connecticut high school tech teacher professional development training, based on our existing incumbent worker training workshops. High school tech instructors from seven Connecticut school districts were in attendance.
As we move into 2022 and monitor the winding-down of the COVID pandemic, our training activity level is up, providing a hopeful sign of a very busy year. To date we have 20 confirmed bookings for workshops through May 10. If that pace continues through the end of 2022, we project completing around 60 workshops with 600 trainees. This pace approaches the pre-pandemic levels of 2018 and 2019, and we will be adding the additional online activity with the 180 Skills asynchronous courses.
In addition to the online training platform, we will be adding several new items to our course offerings. Director of Advanced Manufacturing Laboratories and Continuing Education instructor Les Sinnock has authored a four-hour, one-day workshop titled “Basics of Machining 1.” This course focuses on fundamentals of machining that include Cartesian coordinates with multiple axes, numeric control (NC), understanding mill machine tooling, feeds and speeds, materials, and loading stock and setup. We are also working on concepts for workshops on geometry for manufacturing workers, Fanuc robot programming and operation basics, incumbent worker training systems and methods for manufacturing, and Industry 4.0 with a particular focus on Model based definition (MBD).
Our client companies have also inspired new ways to structure training. We have created a new hybrid model of training tracks in a system that combines live workshops with asynchronous online training from 180 Skills. The training includes tracks on onboarding/apprenticeship, quality, production, and general management. We have partnered on a similar program with one of our client companies who created a guided online training program for their workers, and integrated our live workshops to compliment and reinforce the online content. The effectiveness of the program was evident and we decided to emulate it.
If you are considering manufacturing training programs to upskill your employees, we invite you to write or call us at Goodwin first so that we can help we can guide you through building an effective training program. You may find that many of the training topics you need are workshops in our current catalogue, ready to offer at little to no cost to your company. We are happy to come to your facility to talk and to train. We can train in your facility or in our 44-foot mobile lab. We roll up to your location, your workers come in for four hours, and then go back to work.
For more information, please contact:
Mel Hoben, Director of Workforce Development, mhoben@goodwin.edu or Kyle Zachary, Continuing Education instructor, kzachary@goowin.edu.
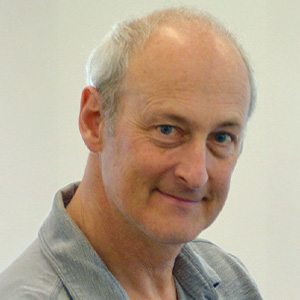
Les Sinnock is the Lead Quality Lab Technician and Continuing Education Instructor at Goodwin University’s School of Business, Technology, and Advanced Manufacturing. He is an industry veteran of 42 years and has been employed in the engineering technical trades at electronics, automation, brewing, R & D of fuel cell, and space flight technologies.
lsinnock@goodwin.edu